Oil Seals | High-Quality for Industrial Applications | A2Z SEALS
Quality Seal Kits takes pride in offering a diverse selection of sealing solutions to meet the demands of various industries. We design our wide range of high-performance oil seals to ensure efficient and reliable performance in a multitude of applications.
Unveiling the Dynamics of Oil Seals
Oil seals, often regarded as the unsung heroes of machinery, play a critical role in preventing the escape of fluids and contaminants in a wide array of industrial applications. As inconspicuous as they may seem, these seals are indispensable for maintaining the efficiency and reliability of rotating equipment. In this comprehensive exploration, we embark on a journey through the intricate world of oil seals, unraveling their types, detailed descriptions, working principles, and the fundamental functions that make them integral to the seamless operation of mechanical systems.
Types of Oil Seals:
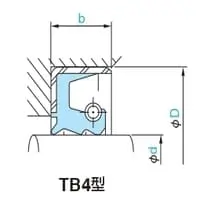
Oil seals, also known as rotary shaft seals or grease seals, come in various types, each designed to address specific challenges and applications. Understanding the distinctions among these types is crucial for selecting the right oil seal for a given purpose.
1. Single-Lip Oil Seals:
Single-lip oil seals feature a single sealing lip that makes contact with the rotating shaft. This type is commonly used in applications where moderate sealing efficiency is sufficient. They are straightforward in design and are suitable for sealing oil or grease in relatively low-pressure environments.
2. Double-Lip
Double-lip are an enhanced version of the single-lip design, featuring an additional lip on the inner side. This double-lip configuration provides improved protection against contaminants and enhances the overall sealing effectiveness. It is commonly employed in applications where a higher level of sealing performance is required.
3. V-Ring
V-ring seals, also known as axial face seals, have a unique V-shaped profile. They are particularly effective in sealing rotating shafts in applications with axial movement. V-ring seals excel in preventing the ingress of contaminants and are commonly used in a variety of industrial settings.
4. Mechanical Face
Specialized seals, known as mechanical face seals or floating seals, find application in heavy-duty and high-load scenarios. These seals comprise two mating metal faces that form a robust seal. Construction machinery, mining equipment, and various heavy-duty applications commonly use mechanical face seals.
5. Spring-Loaded Oil Seals:
Designers create spring-loaded oil seals with an internal spring that applies constant pressure on the sealing lip, ensuring continuous contact with the shaft. This design effectively compensates for shaft runout and variations in operating conditions. Manufacturers apply spring-loaded seals in automotive engines, gearboxes, and hydraulic systems.
Understanding the construction and components of oil seals is vital for comprehending their overall functionality and efficiency in sealing applications.
1. Sealing Lips:
The sealing lip, in direct contact with the rotating shaft, constitutes a critical component of an oil seal. Typically made from a durable elastomeric material such as nitrile rubber or fluorocarbon rubber, manufacturers choose it for its wear resistance and compatibility with the sealed fluids.
2. Metal Case:
The metal case surrounds the sealing lip and provides structural support to the oil seal. It is usually made of steel or other alloys, offering rigidity and protection to the inner components. The metal case also facilitates easy installation and retention within the housing bore.
3. Spring:
Spring-loaded oil seals incorporate an internal spring to ensure continuous contact between the sealing lip and the shaft. The spring provides the necessary radial force, compensating for variations in shaft runout and maintaining an effective seal under different operating conditions.
4. Rubber or Elastomeric Materials:
For the overall performance of the oil seal, the choice of elastomeric materials for the sealing lip plays a crucial role. Commonly used materials, such as nitrile rubber, fluorocarbon rubber (Viton), and ethylene propylene diene monomer (EPDM), offer specific advantages in terms of temperature resistance, chemical compatibility, and flexibility.
5. Dust Lips and Wipers:
Some oil seals may include components like dust lips or wipers, which prevent contaminants such as dust, dirt, and moisture from entering. Additionally, this enhances the longevity of both the oil seal and the components it protects.
This detailed description of oil seal components lays the groundwork for understanding their working principles and functions. In the subsequent sections, we will delve into how these components interact and contribute to the effectiveness of oil seals in various applications.
Motor Seals & Kits
We design our motor seals to maintain optimal functioning of your motors. These kits comprise a range of oil seals that we engineer specifically to endure the requirements of motor applications, guaranteeing longevity and reliability.
Quality : The Preferred Choice
Why choose our seals?
- Superior Performance: Our oil seals are crafted from high-quality materials to ensure
exceptional performance in challenging environments. - Comprehensive Range: From oil seals to PTFE seals, hub seals to cassette seals, we offer an extensive
range to fulfill diverse sealing requirements. - Reliability: Our seals are meticulously assembled, ensuring that you receive all the necessary seals
for your specific application, eliminating guesswork and streamlining maintenance. - Expertise: As a trusted manufacturer, assembler, wholesaler, dealer, retailer, trader, and stockist
of seal kits, we bring years of experience to the table, guaranteeing products of the highest standards. - Competitive Pricing: We understand the importance of cost-effectiveness. Our seal kits offer exceptional
value without compromising on quality.
Contact Us Today
Oil Seals Oil Seals
Radial oil seals are made of ptfe, rubber, viton or Teflon sealing lip, a spiraled tensioning spring, metal case and an internal case. Our Oil Seals oil seals prevent hydraulic oil, lubricants, chemicals or water from escaping, and dirt and dust from entering a machine.
Manufacturers of oil seals
Imported oil seal Type
- Oil Seal
- Single Lip
- Double Lip
- Shaft
- HUB
- Cassette
- Gear Box
- Pump
- Engine
- Motor
- PTFE
- Hydraulic Cylinder
- O Rings
Oil seal kit applications
- Boom
- Dipper
- Arm
- Slew
- Bucket
- Main pump
- Track Adjuster
- Dump
- Back Lift
- David Brown / Parker Pump
- Blade
- Excavator
- Lift
Varied profiles of oil seals
- TC
- TB
- DB
- TCN
- SB
- SA
- SC
- TA
Original Equipment Manufacturer
A2Z Seals offers a full line of replacement oil seal repair kits comprising of varied types and sized used by OEMS, such as Komatsu, Hitachi, Caterpillar, etc. We also offer oil seals used in industries like, cement, mine, steel, coal, sugar and oil.
Chemical Resistance, Cost-Effective, Custom Sizing Options, Diverse Material Options, Easy Installation, Global Availability, High-Temperature Resistance, Industry Compliance, Innovative Sealing Solutions, Leak Prevention, Long Service Life, Low Friction Design, OEM Compatibility, Precision Machining, Rapid Delivery, Versatile Applications.